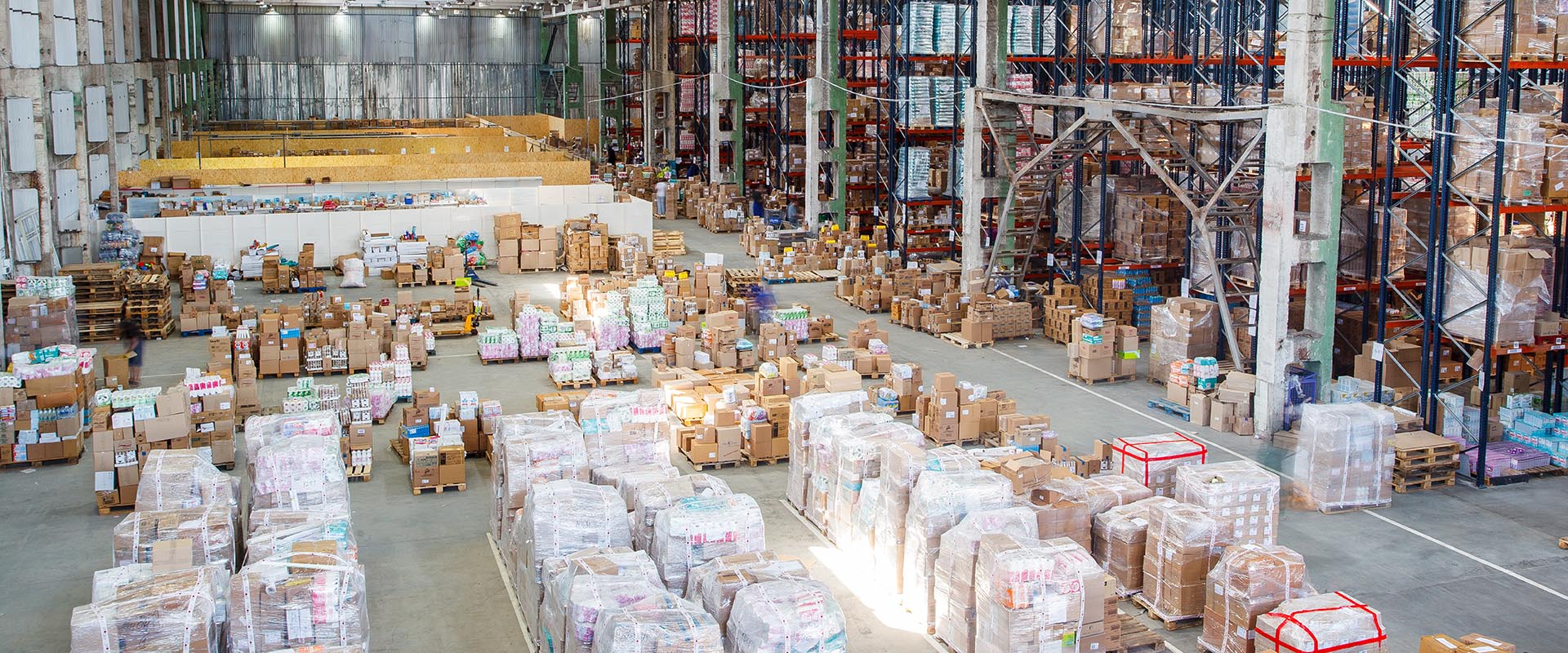
One of the biggest supply chain stories from 2022 was the lack of available warehouse space. After being burned by supply chain issues, which caused widespread inventory shortages at the height of the COVID pandemic, businesses started stockpiling products to try to meet demand and ensure customers weren’t disappointed.
However, thanks to inflation worries and COVID stimulus ending, consumers didn’t buy as much excess inventory as businesses had hoped. This led to a shortage of warehouse space. Some retailers had to resort to selling goods at a steep discount in order to move their overstock.
Further, because of the laws of supply and demand, warehouse prices have soared as space has become harder to find. Even retailers without excessive extra product are paying more to store the inventory they have.
Even in the best of times, inefficient warehousing processes can create a space crunch. However, there are a few warehouse storage solutions that managers can do to maximize the space being used in each facility.
Collaborate with suppliers.
Your supplier relationship is crucial to your success and should go beyond just sending them a purchase order. Their inventory struggles are your inventory struggles. So, for both of you to keep up, it may be helpful to share things like demand forecasts and other important information. This helps your suppliers plan for potential upticks in demand, so they have the material and labor necessary to meet your order volume.
You should also take a look at supplier performance. Do you have one or two suppliers who aren’t performing as well as they used to, or as well as your other suppliers? Talking to under-performing partners may uncover challenges you can help them solve, or help you identify partners you need to drop in favor of suppliers who can better meet your needs.
Having suppliers on deck who can quickly fulfill orders ensures you don’t have a whiplash effect of understock, then overstock, that overwhelms your warehouse.
Build up, not out.
One of the easiest ways to increase available storage in your warehouse is to extend your racks upward (provided you have the right-sized uprights and base plates to handle it). Another option is building a mezzanine above floor-level operations like shipping/receiving. Look at the space above shipping/receiving doors – could you fit pallets of supplies, slower-moving inventory or a staging area there? Using all the vertical space available in your warehouse extends your inventory without requiring a building expansion or finding a new, larger facility.
Even if you can’t build upward, there are still creative warehouse storage solutions you can use to maximize space. For instance, examine your aisle spacing between racks. Can you narrow those aisles without compromising your ability to reach inventory? Will your lift equipment be able to work in a narrower space so you can take advantage of more of the warehouse footprint? Consider these questions to see if you can create additional space if you are unable to extend vertically.
Take full advantage of your warehouse management system (WMS).
Your WMS should be able to do more than just help you stage and ship orders. It should also provide warehouse storage solutions, including a directed put-away feature that identifies the best place for each pallet to optimize your available space. Many operations let workers put pallets away where they think it’s convenient, but those locations may not make the best use of your racking.
Your software also helps you identify the flow of all your products, so you can put faster-moving inventory in the most convenient places. This reduces the amount of travel needed to pick and pack your most popular products, and saves the higher, farther and more out-of-the-way spaces for slower-moving goods.
Pull in temporary storage for peak seasons.
If you’re short on budget, upgrading to a bigger facility may be out of the question. However, you still have to meet demand during your busiest seasons. Demand forecasting may help you identify when those seasons are and which products to stock up on, but you’ll need room for all that inventory.
In this case, pulling in extra trailers to temporarily hold your overflow may be a great option. You’ll have demurrage charges for those trailers, but when you only need the extra space once or twice a year, it’s a more economical option than shelling out for a newer, bigger warehouse.
As consumer spending settles, warehousing space will hopefully become more available and give supply chain operations a breather. Even when things return to some semblance of normalcy, however, using these warehouse storage solutions to maximize your storage capacity can help you keep costs down until warehouse prices aren’t at such a premium.