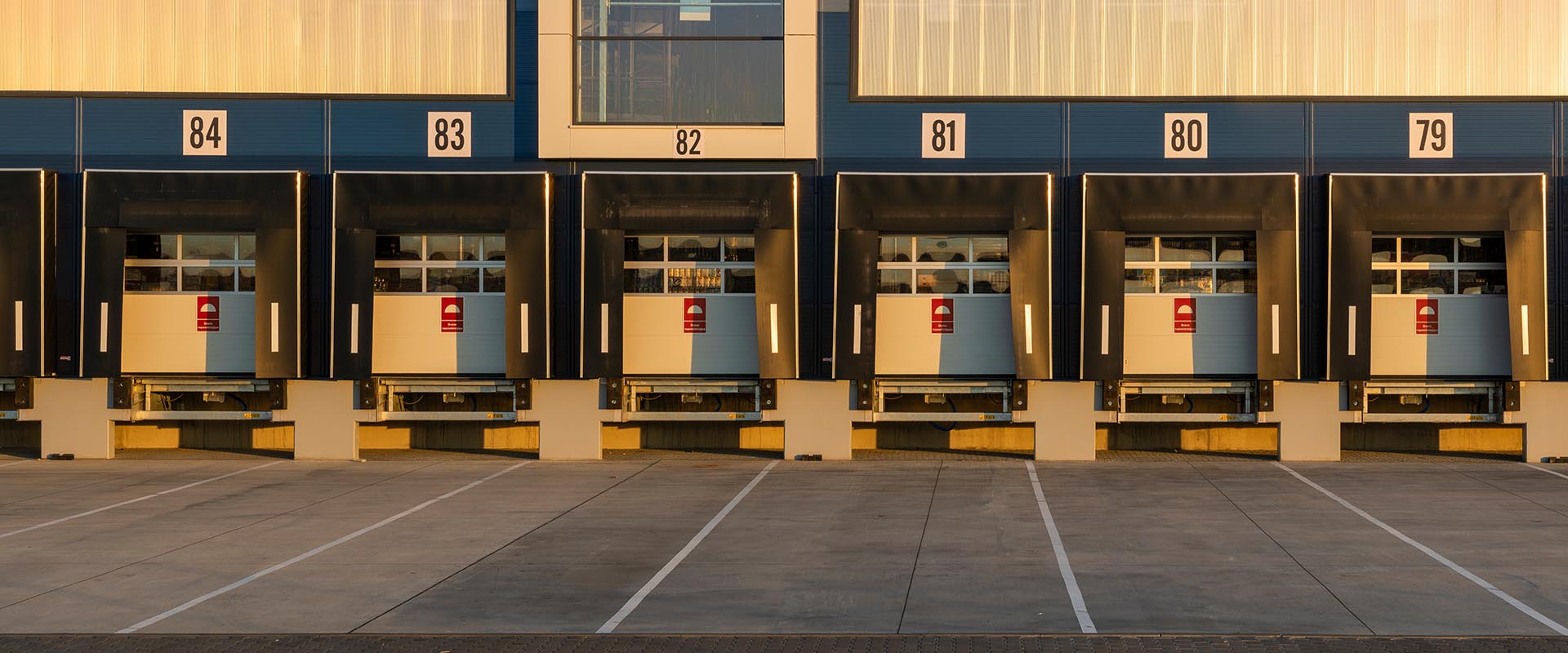
What Causes Supply Chain Disruptions?
From natural disasters to geopolitical situations (like the war in Ukraine or rising tensions with China), there are several forces that can have a significant impact on transporting materials and products from origin to destination. Consumers also impact your operations by changing their demand patterns for various reasons. For example, as we’ve come out of the Covid pandemic, the looming fears on customers’ minds are inflation and a possible recession.
Weathering market shifts can feel like sailing in a hurricane. Even in quieter times, supply chain operations are often the most expensive part of a business’s operating costs, so finding ways to streamline, optimize and reduce spending can make all the difference.
How to Be Prepared If and When Disruptions Occur
If you’re looking for ways to make your operation more flexible and better able to handle supply chain disruption, these five tips can help.
1. Analyze the weak spots in your supply chain
It may seem obvious, but reducing vulnerabilities in your supply chain starts with knowing where those vulnerabilities are. The best place to begin is mapping your entire supply chain and tracking your historical and current data to get a complete view of your material and product journey.
Using this information, you can spot areas where the process slows (or even breaks) down. For example, maybe you’re seeing slow movement out of a particular distribution point or carrier. How can you adjust to either optimize that part of the product flow or move part of your capacity to a different facility or transportation partner?
There are a lot of different points along a supply chain where inefficient processes can slow things down, and a slowdown at any time can cause even bigger bottlenecks down the line. Spotting these points and finding solutions for them now can make a huge impact on your operation the next time a disruption happens.
2. Diversify suppliers
One of the most vulnerable points in less mature supply chains is relying on just a few suppliers, or worse, just one. If that supplier experiences a problem, suddenly your entire operation is unable to maintain production deadlines.
When adding new suppliers to your network, do some careful vetting to make sure you’re reducing your supply chain risk, not adding to it. A few important questions to ask when looking at a new vendor include:
- Have they experienced supply chain disruption in the past few years?
- If so, how did they handle it, and how long were they unable to meet demand?
- If so, how did they handle it, and how long were they unable to meet demand?
- Are they located in an area that’s vulnerable to geopolitical or weather/climate challenges?
- Do they have a history of violations (compliance or other) that could put your operation at risk?
3. Talk to your customers
Whether your customers are distributors, retailers or end consumers, communication is crucial. End consumers are more demanding than ever when it comes to on-time delivery, so notifying them immediately if there’s a problem can help keep them from losing trust in you.
As soon as you notice the potential for a slowdown or insufficient inventory, let your customers know what’s happening and what you’re doing to fix it. As we saw during the pandemic, sometimes shortages are unavoidable, but transparency and the way you inform your customers of these shortages can make all the difference to customer loyalty.
4. Build more flexibility into your operation
Diversifying suppliers is just one part of building a more resilient supply chain. To make your operation as disruption-proof as possible, you need to build flexibility throughout your whole product journey. Important actions to take now include:
- Gain visibility into your materials and product movement. Real-time tracking from supplier to carrier to distribution center to final destination helps you not only better manage production schedules but also enables you to give customers the transparency they expect.
- Improve your demand planning. Analyzing your historical data will help you predict which products need to be prioritized throughout the year to meet demand. You should also identify which products are the most important to your customers. That way, when a disruption occurs, you know which products to prioritize over others.
- Build contingency plans. One thing the Covid pandemic did for supply chains was highlight some of the biggest weak spots: congestion, labor and driver shortages, skyrocketing costs and more. With these past challenges in mind, you can start building a plan to mitigate these problems for future disruptions, such as listing different shipping options and contracting with a variety of partners to help get your goods delivered without breaking your budget.
5. Partner with fulfillment solution providers
In addition to lining up a variety of partners, you should consider adding an experienced freight brokerage or transportation manager to your list. By partnering with a brokerage that has a solid network and offers robust technological solutions, you’ll have a much easier time optimizing your supply chain.
Leaning on your brokerage’s expertise can help you cut costs, improve the efficiency of your supply chain and streamline your operations to keep things moving even during challenging times.
Handling supply chain disruptions and market shifts starts well before the next disruption occurs. Be proactive and analyze your supply chain now, make a plan for what you’ll do if disaster strikes and lean on experienced partners to help you ensure a smooth operation, no matter what the market throws at you.
Need help preparing for the next supply chain disruption?
Ryan Transportation has the experience, expertise and technology to help logistics managers plan for unexpected shifts in the industry. Contact us to see the difference our team can make for your business.